Porosity in Welding: Identifying Common Issues and Implementing Finest Practices for Prevention
Porosity in welding is a pervasive concern that usually goes undetected up until it causes substantial issues with the stability of welds. This usual defect can compromise the strength and resilience of welded frameworks, posturing security risks and leading to pricey rework. By comprehending the root creates of porosity and applying effective prevention approaches, welders can considerably enhance the top quality and reliability of their welds. In this conversation, we will certainly check out the key variables contributing to porosity development, examine its detrimental impacts on weld performance, and talk about the very best methods that can be adopted to decrease porosity occurrence in welding processes.
Typical Sources Of Porosity
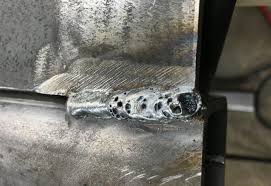
An additional frequent wrongdoer behind porosity is the presence of pollutants on the surface area of the base metal, such as oil, grease, or rust. When these impurities are not effectively eliminated prior to welding, they can vaporize and end up being entraped in the weld, creating problems. Using filthy or wet filler products can present pollutants into the weld, adding to porosity problems. To minimize these typical root causes of porosity, extensive cleansing of base metals, proper protecting gas option, and adherence to optimum welding specifications are vital techniques in accomplishing high-quality, porosity-free welds.
Impact of Porosity on Weld Quality

The presence of porosity in welding can significantly compromise the architectural stability and mechanical properties of bonded joints. Porosity creates gaps within the weld metal, weakening its total toughness and load-bearing capability. These voids work as anxiety concentration factors, making the weld extra at risk to splitting and failure under used tons. Additionally, porosity can lower the weld's resistance to rust and various other ecological factors, better decreasing its longevity and efficiency.
Welds with high porosity levels often tend to display lower effect stamina and lowered capacity to flaw plastically prior to fracturing. Porosity can restrain the weld's capacity to properly send pressures, leading to early weld failing and prospective security dangers in important frameworks.
Finest Practices for Porosity Prevention
To improve the structural stability and high quality of welded joints, what particular steps can be executed to minimize the occurrence of porosity throughout the welding procedure? Porosity prevention in welding is essential to guarantee the stability and strength of the final weld. One reliable method is appropriate cleaning of the base steel, eliminating any contaminants such as corrosion, oil, paint, or wetness that could lead to gas entrapment. Ensuring that the welding tools remains in good problem, with clean consumables and appropriate gas circulation rates, can also dramatically decrease porosity. Additionally, maintaining a secure arc and controlling the welding criteria, such as voltage, present, and travel speed, helps create a consistent weld explanation swimming pool that reduces the threat of gas entrapment. Utilizing the correct welding method for the specific product being welded, such as changing the welding angle and weapon setting, can even more prevent porosity. Routine inspection of welds and instant removal of any type of concerns identified throughout the welding procedure are vital techniques to stop porosity and produce high-grade welds.
Significance of Correct Welding Techniques
Executing appropriate welding methods is vital in making sure the architectural stability and high quality of welded joints, developing upon the foundation of reliable porosity avoidance procedures. Welding methods directly affect the overall strength and resilience of the welded framework. One vital element of appropriate welding methods is preserving the appropriate heat input. Too much warmth can cause boosted porosity due to the entrapment of gases in the weld pool. Alternatively, inadequate heat may cause incomplete fusion, producing prospective powerlessness in the joint. In addition, making use of the proper welding specifications, such as voltage, present, and take a trip speed, is important for accomplishing sound welds with marginal porosity.
Furthermore, the option of welding procedure, whether it be MIG, TIG, or stick welding, ought to straighten with the specific needs of the project to make sure optimum results. Appropriate cleansing and prep work of the base metal, in addition to picking the right filler material, are likewise crucial elements of skillful welding techniques. By adhering to these finest techniques, welders can minimize the risk of porosity formation and create high-grade, structurally audio welds.
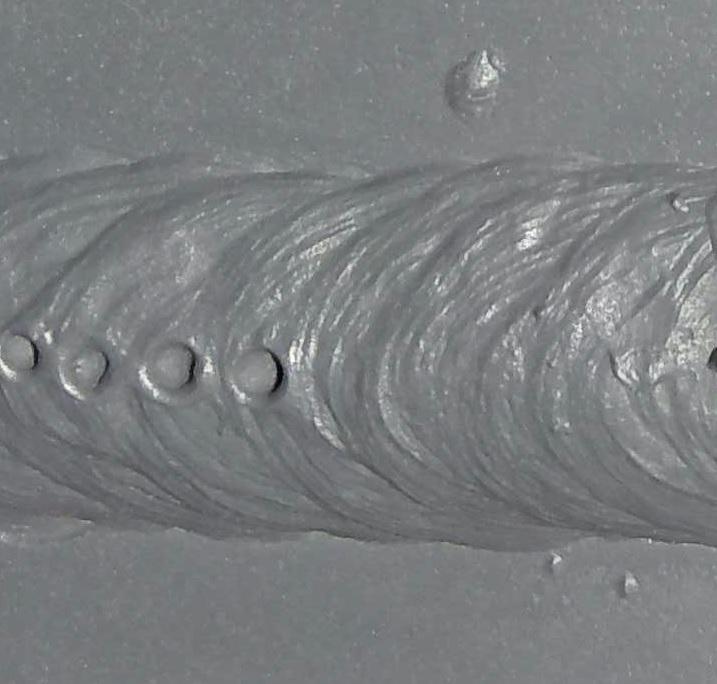
Testing and High Quality Control Procedures
Checking treatments are vital to spot and avoid porosity in welding, guaranteeing the strength and durability of the last product. Non-destructive screening techniques such as ultrasonic testing, radiographic screening, and visual inspection are generally utilized to identify prospective problems like porosity.
Post-weld inspections, on the other hand, assess the final weld for any type of flaws, consisting of porosity, and verify that it satisfies specified standards. Executing an extensive quality control plan that consists of thorough screening treatments and assessments is extremely important to lowering porosity issues and making certain the total top quality of bonded joints.
Final Thought
To conclude, porosity in welding can be go a common concern that influences the high quality of welds. By determining the common sources of porosity and carrying out finest practices for avoidance, such as proper welding techniques and screening steps, welders can guarantee top quality and reliable welds. It is important to prioritize avoidance methods to minimize the incident that site of porosity and maintain the honesty of bonded structures.